Quality Engineering

Quality Objective
1. Zero failure cost.
2. Zero quality defect.
3. Customer satisfaction completely.

Quality Policy
1. Customer oriented.
2. Entire personnel involved.
3. Continuously improvement.

The ensure of customer satisfaction
To prevent the recurrence of defects, when products at initial stage we thoroughly solve the foreseeable problem to ensure quality can be quarantee.

The observance of the source management
To prevent the recurrence of defects, when products at initial stage we thoroughly solve the foreseeable problem to ensure quality can be quarantee.

To promote the process improvement
Carry out a concept of next stage is customer.
No accept of non-conformance, No manufacture of non-conformance, No produce of non-conformance.
Quality Declaration
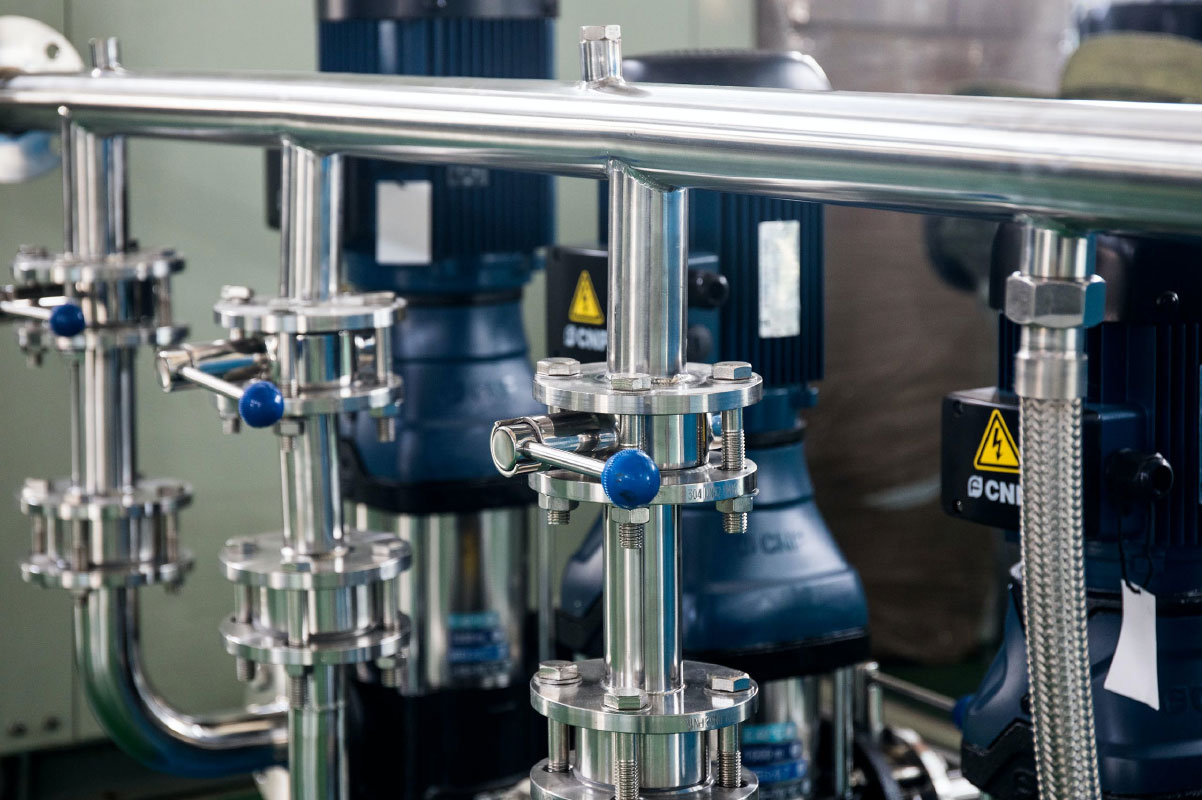
Quality Management
Regarding quality control, our effective in-house QC reduces defects and prevents defective items from passing to the next phase, and thus saving time and ensuring quality. Final surface quality inspection is fully automated and is guaranteed by 3D Inspection System.
Procedures/testing Details: Our quality control encompasses:
1. Incoming inspection
a. Rheometer testing of batch compound mixing
b. Dimension inspection of first molding and after oven curing
c. 100% surface visual inspection
2. Final inspection
a. Automated surface and dimension as requested by 3D Inspection System
b. Data analysis and statistics to verify the improvement and effectiveness.
Through PR, ECR, ECN internal non-conformance recording, quality is expected by designing and not by inspection.
We also understand the importance of in-process QC in finding defects from starting points, and as such we require self-inspection in each process.
Assist customers to create a win-win situation
WellMore Group Inc.

Call us today
+886-2-2968-2485
or